Tired of unexpected asset maintenance costs? Learn about the advantages of a CapEx facility management strategy.
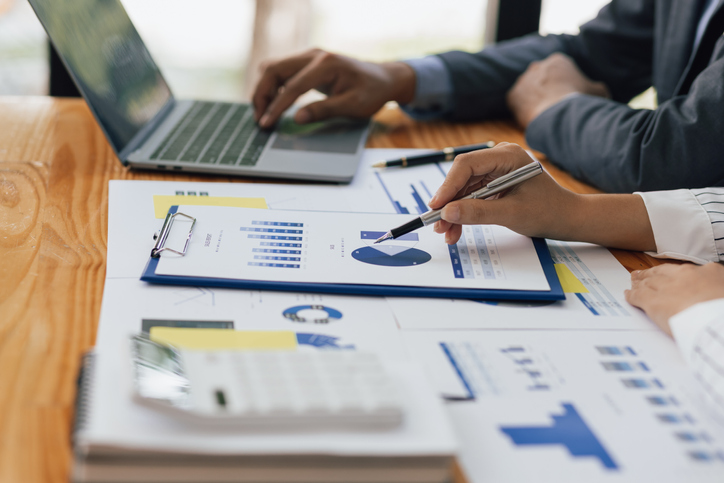
Tired of unexpected asset maintenance costs? Learn about the advantages of a CapEx facility management strategy.
Learn how to become a vendor for facility maintenance with CLS Facility Services. Explore the advantages of partnering with an aggregator today.
Exploring facility management companies? Learn about self-performing and aggregator service providers — and why one is better than the other.
Discover the 5 commercial storage and facilities services that turn cost centers into optimized operations with enhanced security and efficiency.
Electrical infrastructure powers modern medtail operations. Learn why specialized healthcare electrical maintenance is critical for clinic success and patient safety.
Protect your financial institution with five essential fire and life safety services to create a truly proactive protection strategy. Learn more from CLS Facility Services.
Explore 6 essential components of an effective retail store HVAC management program from the experts at CLS Facility Services. Read here for all the details.
Specialized healthcare facilities management for clinics and medtail establishments is critical for operational efficiency.
With CLS Facility Services, you can turn bank building maintenance from reliant on reactive repair cycles to proactive facility management.
Tina joined CLS in 1998 in the position of Billing Clerk and will be celebrating her 27th anniversary this year. Meet her here.
Need some guidance on post-holiday retail facility maintenance? Ensure you’re prepared for the year with this overview from CLS Facility Services.
Navigating quick service restaurant facilities management can be complex — unless you know where to look for the right support.
In financial services and bank facilities management, physical location conditions dramatically impact customer experiences.
LED’s Rise and Improving Cost Efficiency Lighting codes and standards have evolved for decades since their creation, and where we stand in 2025 is no exception. When LED Lighting emerged, it was costly, the technology was unproven, and LED warranties…
Christina Villella, our Vendor Relations Senior Team Leader, has built a 25-year career with our company. Learn why we love her!